The team
The Georgia Tech team consists of residents, interns, and visitors of the Autodesk Technology Center in San Francisco. The residency team consists of Jaime, Ivan, and Drew, who will travel to the Technology Center to implement a digital architecture for machine monitoring in the fabrication spaces. The interns, Lance and Eddie, will be based in San Francisco and will analyze data collected from the instrumented CNC machines to integrate with Autodesk Fusion 360 and enhance its capabilities. Blane, a graduate researcher in Dr. Katherine Fu’s lab, joined the team in San Francisco and met with the shop managers at the Autodesk Technology Center to identify the impact of these and other technologies. Dr. Chris Saldana and Dr. Amit Jariwala also visited to connect GT leadership with the work being done at the Autodesk Technology Center. The team would like to thank Gabby Patin and Mei-yen Shipek (Autodesk Technology Center / San Francisco) and Vanessa Sigurdson (Autodesk Technology Center / Toronto) for facilitating the residency, as well as Olivia Struckman and Al Whatmough for engagements with the Autodesk Fusion Team.
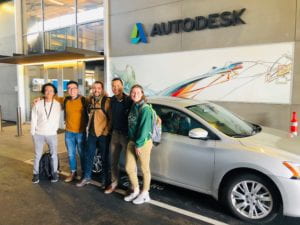
Epilogue
The team hosted Scott Borduin (Autodesk CTO) and Scott Reese (Autodesk Senior Vice President of Manufacturing, Cloud and Production Products) on campus to discuss and review the EPICS program and how we are working together with various stakeholders at the Autodesk Technology Centers and the Autodesk Research organization to advance cybermanufacturing technologies for industry. Thanks to Scott and Scott for taking the time and your support!
Eddie and Lance were also recently featured on the Autodesk Instagram page giving their thoughts on working at Autodesk Technology Center San Francisco. Take a look at this link!
week 10
It’s the team’s final week at Autodesk Technology Center San Francisco and the Residency team returned for multiple briefings and also disassembly of the sensor packs from the machine spaces within the facility. The team also followed up with the Autodesk Research Team on the possibility of deploying sensor packs and advanced analytics for chatter detection in machining processes. Collaborative opportunities will be the subject of future discussions between the two groups later this summer.
Both the Residency (e.g., Ivan, Dr. Saldana) and Intern teams (e.g., Eddie, Lance) gave a final report out briefing to the Autodesk Technology Center in San Francisco and this was simultaneously broadcasted to the other Autodesk Technology Centers. A video of the Residency Team’s pitchout is available on Autodesk’s Vimeo page at this link.
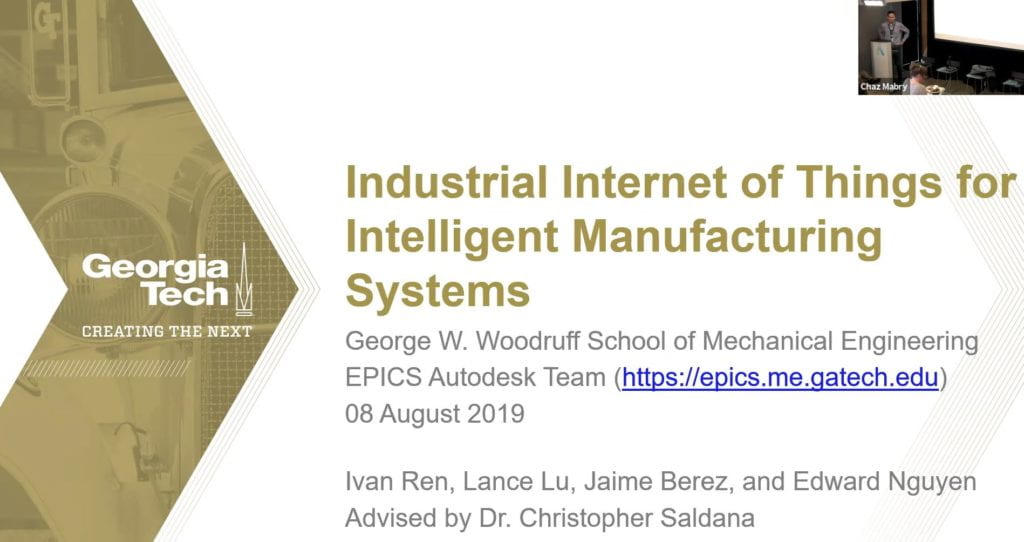
On the Fusion team side, Eddie authored a blog post on Autodesk’s internal engineering site regarding the subject of the Industrial Internet of Things (IIOT). Eddie describes in detail the impact of IOT on the consumer market and what IIOT is doing for manufacturing in this post. He also summarizes the work that has gone on within the Autodesk Technology Center through the collaboration with Georgia Tech. If you’d like to read it, you can find a copy at this link.
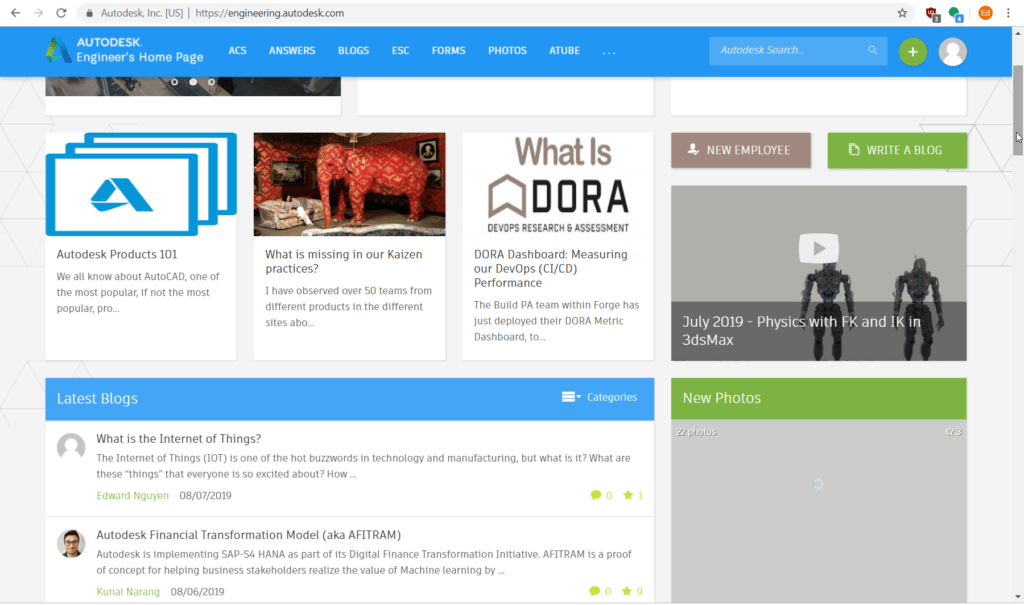
The teams worked with the shop staff to remove the final sensor packs and mobile communications hardware from the machine tools and Autodesk Technology Center workspace. The team also said goodbye to the amazing group of folks supporting the Residency Program and Fusion Team. We’re going to miss this excellent group of folks and look forward to future collaborations!
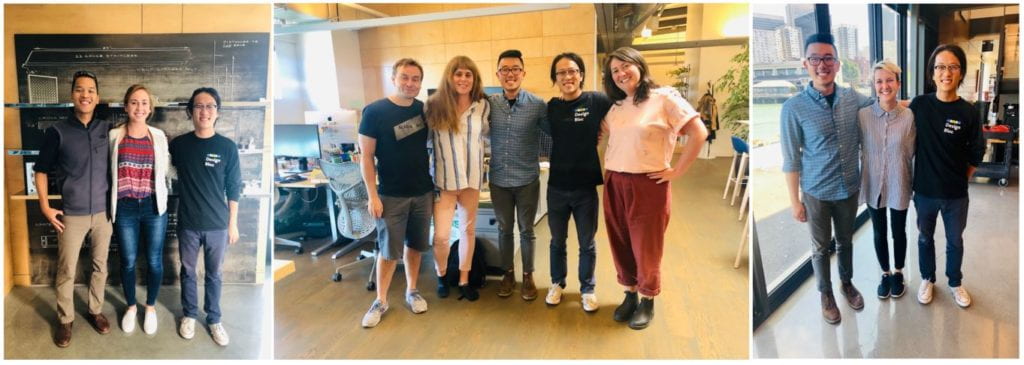
-Dr. Saldana, EPICS Faculty Advisor
week 9
Beep, boop, I’m a robot. This week we hit a few more stretch goals, including starting up a bot on Slack that can automate a bunch of functionality. So far, the bot is able to:
- Give the state of a machine or overview of all machines when queried by a user
- Allow shop staff (shoparones) to “clock in” or out to determine if machines are being used unsupervised
- Send notifications if it detects “chatter” – right now we’re sending artificial triggers but we’re exploring integrating the data we’ve been collecting.

In other machine-related news, we were able to start classifying the data from the accelerometer. This is the same slot test experiment from earlier, now with more detail! The smaller three graphs show data collected from an air pass, then cutting the 5 slots at varying depths, and the third graph is a cleaned up version of the center graph.

When you take a look at the process in 3D, you can distinctly tell where each slot was cut. It’s amazing how clean the graphic turned out – relatively little processing was required to achieve this.
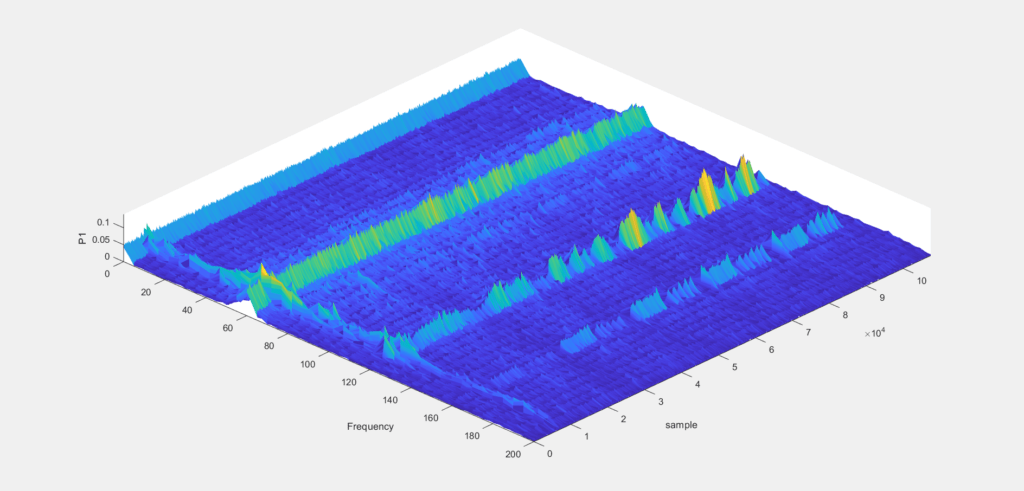
week 8
Chirp, chirp. Chatter, chatter.
One of the more common undesirable phenomena experienced in a machining operation is known as chatter, or when the tool starts vibrating against the workpiece. This is something manufacturers want to avoid at all costs, because it produces a number of negative results:
- A loud, screeching noise
- Poor finish quality on the part
- Reduced tool life
- Increased machine load
We worked to detect and plot chatter so users can be alerted to when it starts happening in order to take steps to reduce or eliminate it.
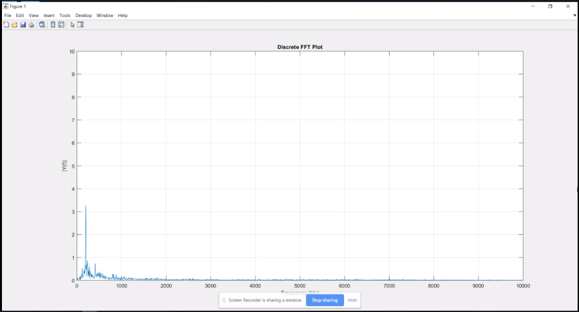
In addition, Lance and I were invited to present to a huge audience (over 100 participants) in a weekly sync-up call hosted by Al and Olivia. They got to discuss their project to a wide audience that included research, end users, and other interested parties. A video recording of this web-based discussion is provided for review at this link.
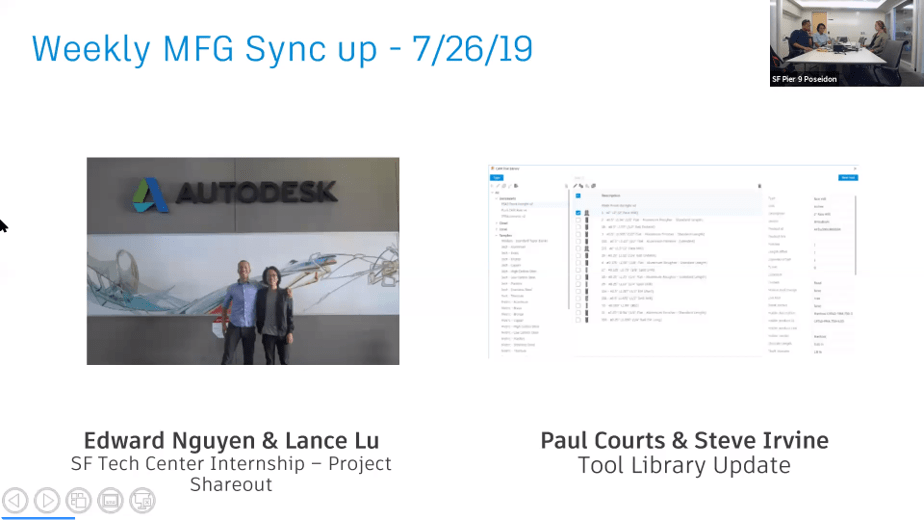
week 7
Things are humming along, literally. We’ve been using the Haas almost every day this week, cutting test parts and collecting data.
Final Assembly of the enclosure
Some of the sample parts we used to get data
week 6
More dashboards! We’ve tweaked the Node-RED dashboard a little more to display more information and to allow a user to switch between machines to see how each one is behaving.
Dashboard is up and running for reporting machine state and signal information
week 5
Data! We were able to get some of our first sensor readings from the Haas. The changes in current draw were easily visible when we plotted the values captured by the current transformer.
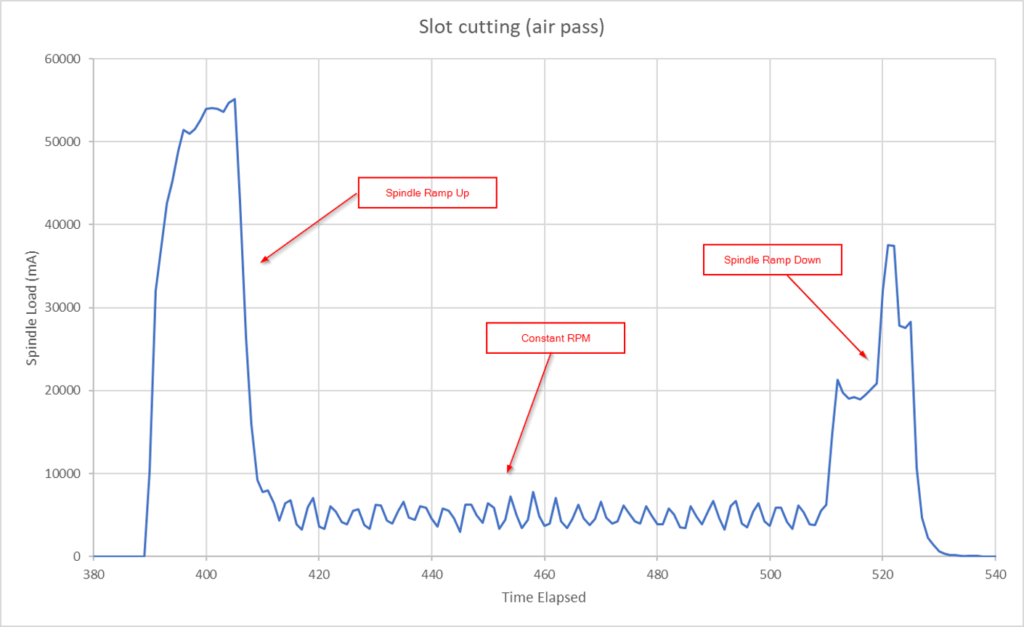
We also started to work on serial communication with the Haas in order to pull more information. The VF2 that is at the technology center still uses an RS-232 or DB25 connection, but hey, we were able to get it to respond!
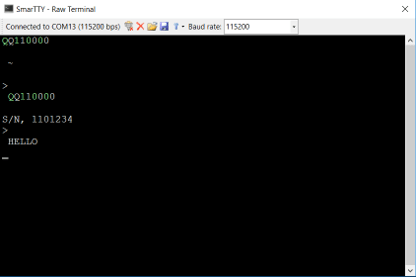
week 4
We can use the Haas! In order to use the machine, we needed to go through classroom trainings as well as an orientation on the machine itself. After going through the instructional portion, we had to create the toolpaths for a certification part and then machine it. Here’s what we got!
Our CAM Fundamentals and Haas controller training parts
You can find reference materials from the Autodesk SF Technology Center’s Instructables Page.
week 3
Trainings galore! The resident team (Ivan, Jaimie, and Drew) and Dr. S. have flown back to Atlanta, leaving Lance and me to steer the ship for the next few weeks. This week it’s all about getting up to speed with the Technology Center’s operational and safety policies for all the machine tools we plan on monitoring.
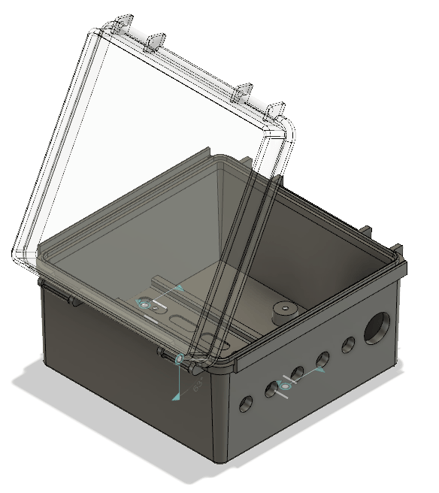
The other big focus for this week is to start writing everything down. It’s still very early in the program, but the amount of material we’re generating is already enormous! I’m starting off by creating a 3D model of the enclosure and all its contents, using Fusion 360 of course. It’s incredibly useful to keep everything in one file rather than bringing in parts from disparate files. The graphics are mostly handled on the cloud, so things run very smoothly on my machine. Here’s where I’ve gotten so far:
-Eddie Nguyen, 2019 Manufacturing and IOT Intern
Week 2
At the beginning of our second week, we met with shop specialists, Joseph Jastreboski, Mary-Elizabeth Yarbrough, Michael Koehle, Ian Kimmerly, and Robb Godshaw early in the morning to install the sensor packs and network hardware. To meet EHS requirements, the shop staff performed a lockout-tagout (LOTO) and personally attached the sensors on all the machines. Over the course of two hours, we instrumented five machines around the shop. The Epilog lasercutter was the first machine to be outfitted with a sensor pack – we installed a current transformer on the power supply of the machine. The Bridgeport knee mill came next and was outfitted with a current transformer and an accelerometer. We encountered a temporary issue with the table saw but we attached an enclosure on the machine to facilitate a future workaround. After the table saw, we moved on to the OMAX waterjet and the Haas vertical mill. The OMAX was fitted with the same sensors as the Bridgeport while the Haas was instrumented with a current transformer, an accelerometer, and a microphone.
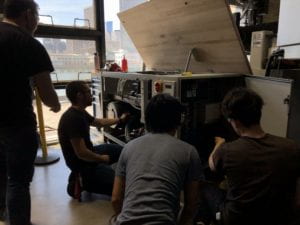
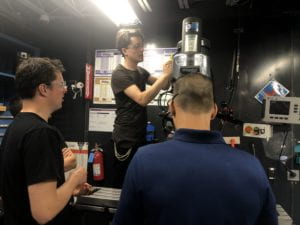
After mounting the hardware, the team checked the database to verify that all of the sensor packs were transmitting properly. During our tests, we discovered that the Bridgeport knee mill was outside the range of our WiFi network so the team set up a secondary network to get the machine online.
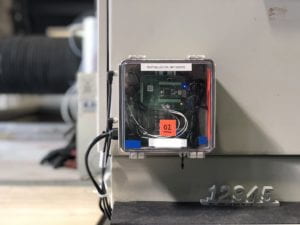
The team also created a dashboard to visualize the data. Dashboard users are able to select from the list of instrumented machines and view the corresponding sensor information in real time.
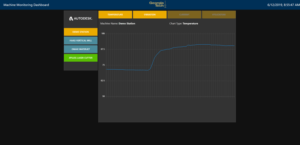
Midway through the second week, we participated in another shop clean and attended the bi-weekly ideas exchange. The ideas exchange is an opportunity for residents to engage with other residency teams and provide status updates on their projects. We discovered that several other groups are working on IIoT applications and we enjoyed speaking with them and learning from their experiences.
The team spent the rest of the week resolving minor bugs in our hardware and calibrating the sensor data to the normal operating states of each machine. With the calibrated data, we can move towards determining machine utilization metrics. The residency team returned to Georgia Tech at the end of the second week.
-Resident Drew Bailey, 2019
week 1
In our first few days at the Autodesk Technology Center in San Francisco, we were able to meet members of the shop team and provide them with an overview of our project. We also connected with some of the other residency teams and learned more about their projects. During this time, we set up the internal WiFi network and tested the connectivity of the data collection devices.
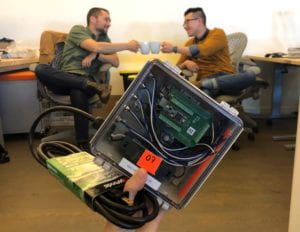
Along with preparing the data collection devices, we also began formulating a plan for the upcoming weeks. We set up meetings with the shop managers and determined the metrics of interest for specific machines.
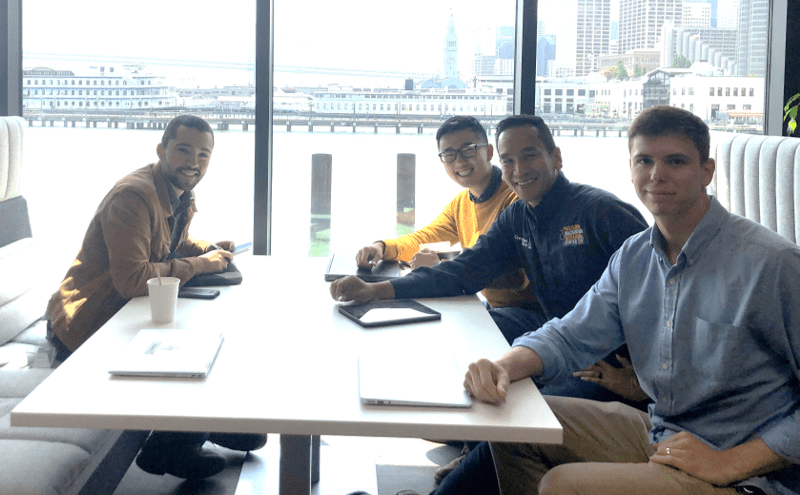
On our third day, we were able to take the General Workshop training course and tour the shop. Before attending general workshop training, we all completed the online Global Workshop Safety training course. We also took a fire extinguisher course which taught us how to use a fire extinguisher in an emergency. This course inspired a friendly competition amongst the group as we took turns trying to get the best time on the fire simulator.
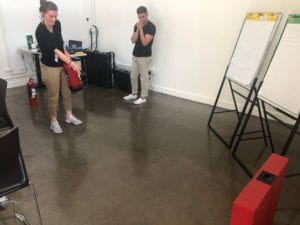
The day following our safety training, we participated in the weekly shop clean. This was an opportunity for everyone to show their respect for the space and interact with residents, interns, and staff members.
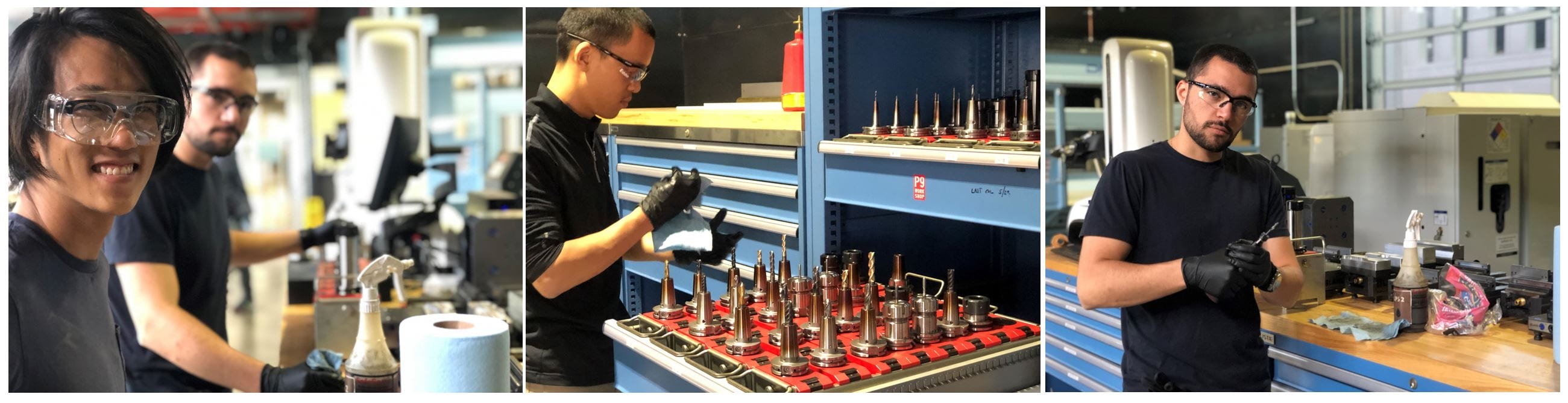
After taking the general workshop training, fire extinguisher training and now cleaning the shop, we are finally ready to get our hands dirty. We inspected the machines we were planning to instrument and determined mounting locations for the sensors. Our sensors include current transformers, accelerometers, thermocouples, and microphones. The machines of interest for our initial deployment were the Haas VF2 vertical mill, Epilog 120W lasercutter, OMAX 60120 waterjet, Bridgeport knee mill, and the SawStop table saw.
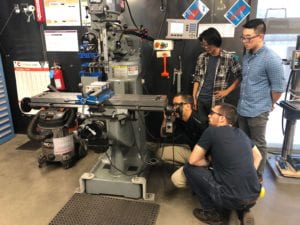
The next step was to provide an implementation plan for approval from the shop team. At this point, Dr. Amit Jariwala came to visit. He toured the facility to determine how the practices at the Autodesk Technology Center can be implemented in The Flowers Invention Studio at Georgia Tech.
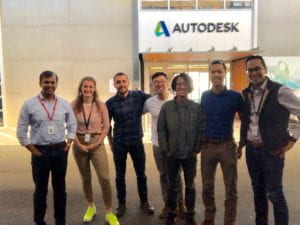
Upon receiving the approval of the shop team, we configured the sensors. The first step to this was to complete the electronics lab training. After completing this training, we began work on constructing the sensors and their enclosures. Each machine required a unique combination of sensors, making organization and documentation essential.
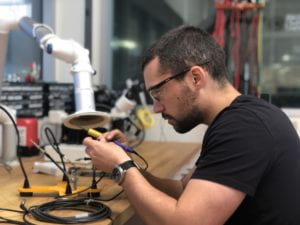
After an exciting first week, we are finally prepared to implement the sensor packs. We are looking forward to the beginning of week two at the Autodesk Technology Center in San Francisco.
-Resident Drew Bailey, 2019